Principle
Through demand analysis, the design objectives are determined, and the equipment skeleton is built by integrating FEMA analysis, simulation analysis, material application, DOE method and DF 'X ' design principle. Then, through the software and electrical control system technology, on the technical platform with high adaptability and expansibility, each part of the structure and components are connected into an organic whole according to the production needs from the bottom layer, and then through the interaction between the bottom layer and the terminal, the interaction and feedback of production and monitoring, internal and external information interaction and traceability, so as to achieve the goal of intelligent precision assembly.
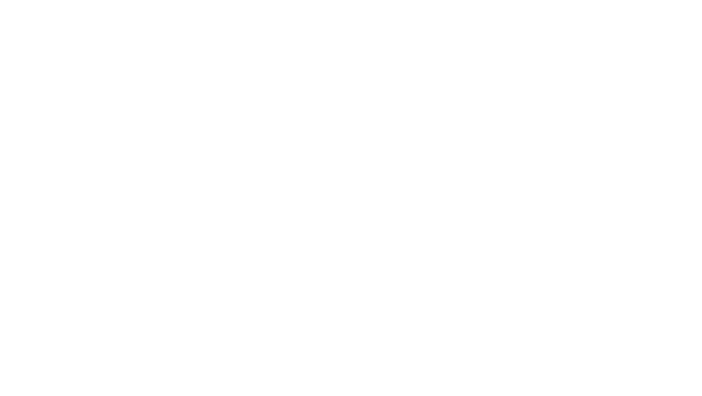
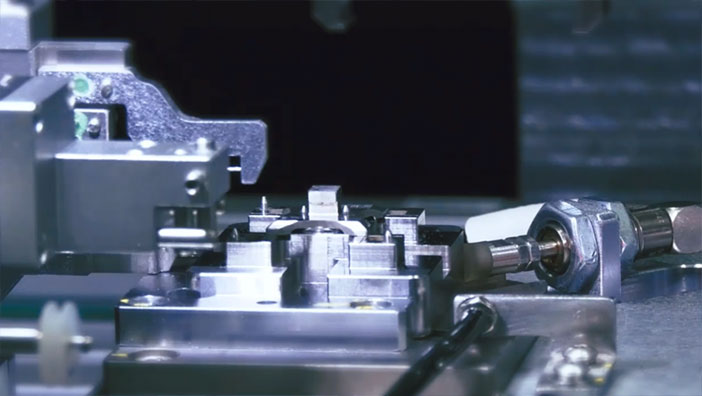
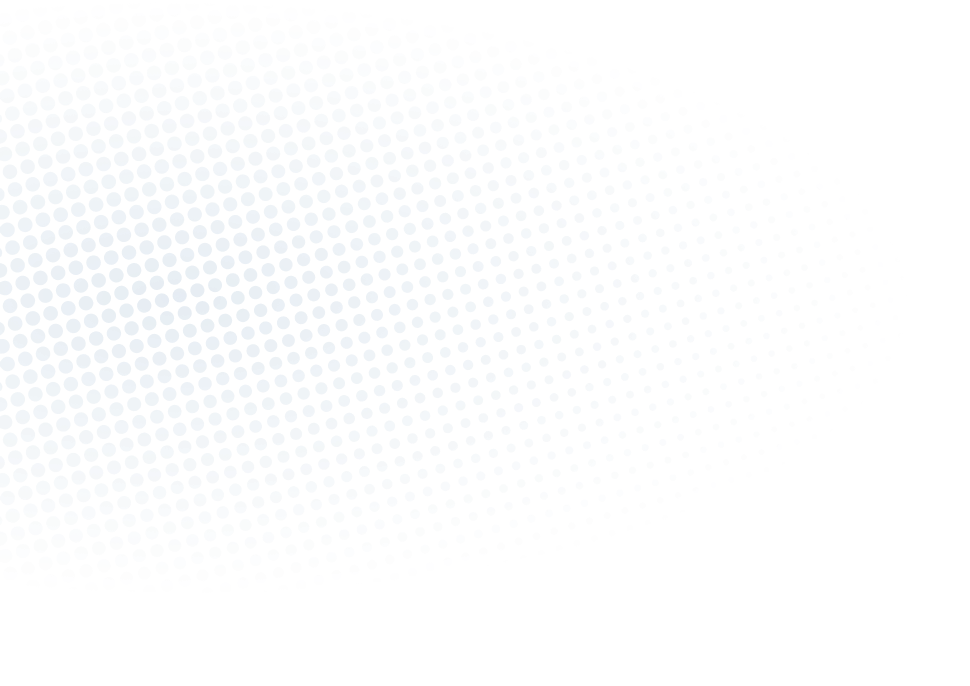
Technical Advantages
-
Advanced fixture and structural design technology
-
Advanced simulation technology and control system technology
-
Advanced fixture and structural design technology
- Considering the requirements of quality, precision, material properties, capacity beat, manufacturing cost, debugging difficulty, stability and life, compatibility and so on.
- The design techniques such as dimension chain calculation, datum design, tolerance analysis, beat decomposition, operation interference simulation and freedom constraint are used to provide the most suitable clamping fixture and structure for different application scenarios.
- In order to meet the quality control requirements in the processing process, it is necessary to study and experiment the materials with high temperature resistance, corrosion resistance, friction resistance, lightweight, refinement, anti-interference and other characteristics.
-
Advanced simulation technology and control system technology
- By using the professional structural mechanics simulation tool, the basic data such as weight, load, material, force, impact and temperature of the mechanical structure are input, and the deformation, vibration, fatigue and stability of the structure are output. According to the weak position in the simulation results, the reasons are analyzed, and the targeted structural strengthening and other optimization design are carried out.
- The hierarchical structure design of software system includes hardware driver layer, core control layer, peripheral control layer, state monitoring layer and human-computer interaction layer. Using standardized module development technology : software authorization management, user management, data acquisition, product management and other functions, custom add and delete modules, improve development efficiency, and realize custom configuration. The system has scalability, operability, controllability, scalability, etc., and constructs a simplified, efficient and high-performance system framework for the rapid development of industrial automation control systems.
Application
-
3C
-
EV power


Products
Products relative to precision assemble
-
EV Battery
-
Electronics
-
Photovoltaic
-
Smart Home
-
Life Sciences
-
Modern Building
-
Transports
-
Sheet-metal Working
-
-
View ProductsAuto Assembly Line of Top Cover
-
Systemized dust and particle prevention treatment.
-
Equipped with self-inspection and foolproof functions for incoming materials.
-
MES system full closed-loop production processing
-
Less spatter, good weld effect and high stability
-
-
View ProductsFull-Auto Prismatic Cell Assembly Line
-
Highly automatic, complete the assembly processes without human intervention
-
Modular design, short changeover time, few parts, low costs
-
Automatic process control with traceable information for the whole processes, which can dock all types of MES systems
-
Digital twin 3D visualization technology, equipment state visualization, intelligent information interaction, improve user experience.
-
-
View ProductsModule Assembly Line
-
Full test of the cell voltage, resistance and thickness to ensure assembly consistency
-
Cell dispensing by two-component nozzle fixed on truss with adjustable glue pressure and mixing ratio and flow monitoring function
-
Unified standards for cell stacking, with high stacking accuracy and one-button switching of stacking modes
-
Visual addressing and off-focus measuring before laser welding to avoid missing welding and incomplete welding, and guarantee welding quality
-
-
View ProductsPACK Assembly Line
-
Completing the transmission of packs between stations by latent traction AGV.
-
Each station can be controlled independently.
-
6-axis machine equipped with two-component gluing heads to glue the bottom cover with adjustable glue pressure and mixing ratio and flow monitoring function
-
MES, full closed loop control system
-
-
-
-
View ProductsAuto Assembly Line of Top Cover
-
Systemized dust and particle prevention treatment.
-
Equipped with self-inspection and foolproof functions for incoming materials.
-
MES system full closed-loop production processing
-
Less spatter, good weld effect and high stability
-
-
View ProductsFull-auto Steel Shell Button Battery Assembly and Packaging Line
-
Compatible with various diameters, thicknesses, tab welding processes and sealing methods
-
The innovative cover plate shell laser welding seal+automatic capping and concentric alignment mechanism has good welding consistency and high yield. The laser seal also makes the energy density of the battery better than the buckle seal.
-
The equipment mainly includes processes like positive and negative electrode tab welding, core into shell, liquid injection (open/small hole), automatic capping, sealing welding, testing, cleaning, AOI detection, liquid leakage detection, etc.
-
The line efficiency can be customized to 20-60 ppm/Line.
-
-
View ProductsMasking Line
-
The machine adopts the simplex station single rack mode, and the number of freely assembled machine matches the UPH.
-
The whole line adopts standardized visual positioning, automatic adjustment of machine track, rapid mutual copying of programs, and can be compatible with 1mm~500mm products to quickly complete line change.
-
Visual dispensing glue, high-speed film pasting, product flap, AOI detection and other processes have been standardized through many technical iterations, and themachine has strong industry advantages in stability and cost.
-
-
View ProductsLaser Glue Removal Line
-
The machine adopts the simplex station single rack mode, and the number of freely assembled machine matches the UPH.
-
The machine adopts square welded frame+air spring roller type open and close door structure, with atmospheric appearance
-
The left and right products are switched with tool-free quick-change structure, and the production switching time of the left and right boards is less than 30min.
-
Precision laser cutting machine innovatively uses 2900W camera to accurately take photos and cut products, generate DWG graphics, 500W CCD secondary positioning, automatically correct the cutting position, maximize the efficiency of laser, cut the waterproof film without damaging the product.
-
-
View ProductsPlanr Transformer Automatic Assembly Line
-
It is applicable to the latest gallium nitride technology PCB integrated transformer, and is a fully automatic production line integrating automatic assembly and testing.
-
Mainly includes core loading, dispensing glue, assembly and inductance testing, curing, fixture unlocking, testing, printing and unloading etc. machines.
-
CORE&PCB realizes fully automatic assembly.
-
-
View ProductsTransformer Automatic Assembly Line
-
More than 50 full-line automated production lines for 3C well-known enterprises are being used for mass production
-
Includes modules such as core automatic loading, AB glue dispensing , core buckling, inductance test, automatic dip-soldering, automatic UV glue dispensing, automatic PIN cutting, automatic laser stripping, taping, hi-pot test, function test,cosmetic inspection, etc.
-
Highly standardized design, low-cost transformation, and rapid mass production of similar products.
-
-
-
-
-
-